From The Leader in Clean Power Production Technologies
Waste-to-Energy Technology — L90 Esbjerg Plant
Success Story
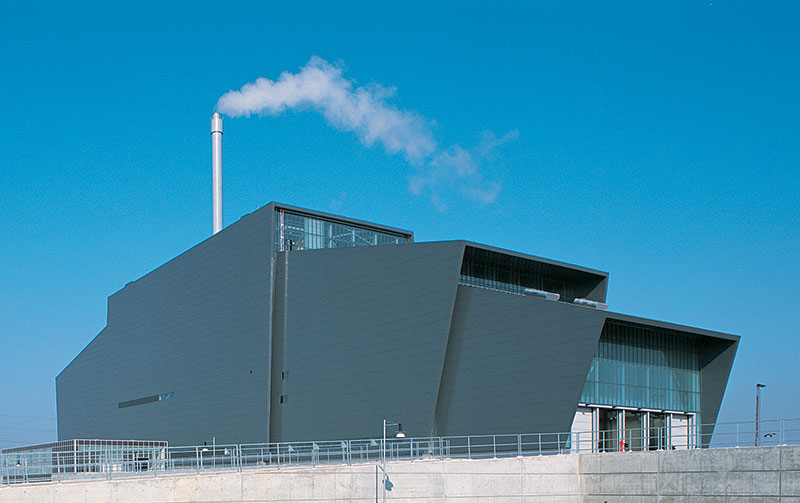
At the beginning of 2001, L90 made a contract for a large new waste-to-energy plant in Esbjerg, Denmark. L90 is a union of 35 municipalities with more than 600,000 inhabitants in the mid-Jutland area and was formed with the purpose of owning and operating the new plant.
Using domestic and industrial waste as fuel, the plant has a design capacity of 24 t/h at a heat value of 11 MJ/kg, corresponding to 180,000 t/year. It is one of the largest plants built in Denmark.
The plant features the latest advances in waste incineration in terms of both boiler and combustion technologies and air and water emissions control technologies. The overall thermal efficiency is 89%.
Babcock & Wilcox Renewable (B&W) was awarded the contract for the supply of the complete incinerator with boiler and control system. The boiler generates high pressure steam for a turbine of 16.5 MWe, and the remaining heat is utilized for local district heating.
Scope of supply
B&W supplied the complete incinerator with state-of-the-art Vølund® technology which included waste crane, feed chute, feed grate and five-section combustion grate, combustion air system, auxiliary burners, ash conveyors for slag and fly ash from the boiler hoppers, feed water pumps with controls. This included a complete steam boiler with boiler drum, vertical furnace with empty passes (pendent structure) followed by economiser and superheater sections made of vertical tubes (standing structure) with cleaning arrangements. Pressurized air and selective non-catalytic reduction (SNCR) systems were also supplied, as were complete control equipment for the whole plant excluding software for turbine, flue gas cleaning, etc.
New technology
The furnace includes cooled wear zone sections at both sides. The furnace and the first boiler pass are cladded with Inconel®, a wear- and heat-resistant alloy, welded directly onto the boiler tubes. Thus, the need for refractory, which requires annual inspection and frequent repairs, is eliminated. Advanced combustion control (ACC) technology with camera monitoring of the combustion was installed for controlling the air supply to the grate in a network, which ensures homogenous combustion throughout the grate.