From The Leader in Clean Power Production Technologies
Waste-to-Energy Technology Case Study
AffaldPlus, line 4 - Næstved, Denmark
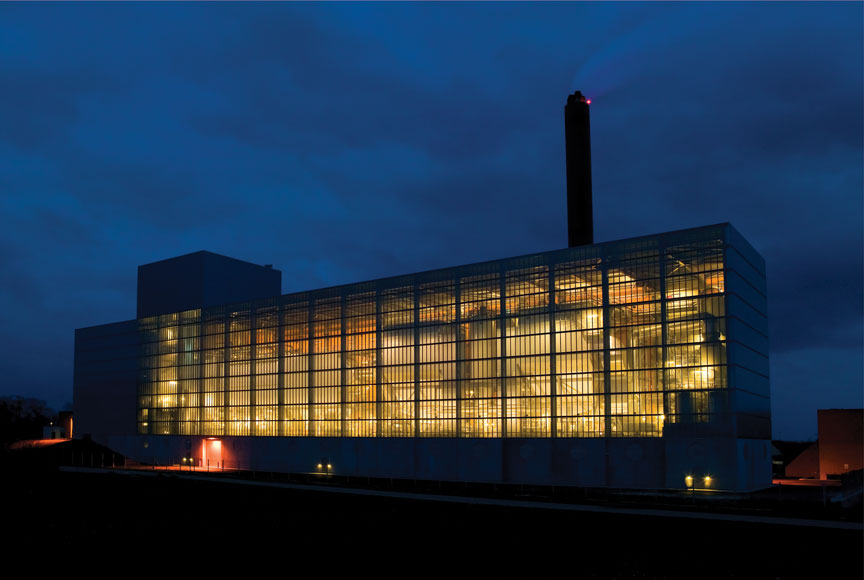
AffaldPlus treats the waste from six municipalities in South Zealand. The waste treatment consists partly of the sorting and reuse of waste and partly of the combustion of waste with subsequent supply of heat to Næstved district heating station and generation of electricity for the supply grid. In total, AffaldPlus supplies 200,000 citizens in the area. In 2006 the plant treated 115,000 tons of waste, resulting in an annual production of 13 MW of electricity and 50 MW of district heating.
Since 1982, Babcock & Wilcox Renewable (B&W) has been the main supplier of combustion systems at AffaldPlus. In 2003, AffaldPlus and B&W signed a contract for the construction of combustion line 4, which has a nominal capacity of 8 t/h and generates steam for an existing turbine.
The new line was handed over to the customer in 2006 – three weeks ahead of schedule. The project is a great example of excellent project management and good cooperation.
Innovative combustion technology
The combustion system combined state-of-the-art VølundTM technology with the latest results from research and development projects within control, CFD and combustion technologies.
The DynaGrate® combustion system is the result of more than 40 years of development. The air-cooled grate is ideal for the incineration of both domestic and industrial waste because of the high efficiency combustion, excellent utilization of energy and good bottom ash quality.
The grate for line 4 is a single-lane grate, which is prepared for conversion into a water-cooled system if this should become necessary some time in the future. DynaGrate is capable of handling all sorts of unsorted solid waste and can be used for co-combustion with biomass.
To control the thickness of the fuel bed, the grate is made up of a number of individually controlled sections. Each grate section has a complete drive mechanism consisting of double-action hydraulic cylinders and control valves.
During grate operation the shafts will alternately turn to their respective extreme positions. The grate bed forms a step-shaped surface where the steps change places, which provides a wave-like movement with a breaking and stirring effect. At the same time the waste is moved forward, and an optimal supply of combustion air is achieved.
- As there is no physical contact between moving grate parts, wear and tear will be limited, and grate exposure to mechanical influence will be minimal.
- Because of the effective mechanical breaking of the waste on the grate, all parts of the waste will be exposed to the heat radiation from the furnace and to the combustion air.
- This, in combination with the effective distribution of air, ensures controlled and effective combustion and stable energy production.
The combustion on the grate is sub-stoichiometric, i.e. with reduced air supply. In this way low temperatures are obtained in the waste bed on the grate, and the melting of the ash into large lumps and the confinement of combustible components are reduced to a minimum. This results in high efficiency combustion and fine-grained ash. The guarantee measurements at AffaldPlus show a typical content of organic matter in the ash of 1/4 to 1/2 % TOC. The slow, continuous movement of the grate produces very little dust and fly ash in the gas flow, resulting in reduced filter load.
VoluMix™ system
B&W's VoluMix™ system was installed at the inlet of the first pass, consisting of a nozzle arrangement that ‘pushes’ the flue gas into two, spiral lines. The purpose of the VoluMix is to ensure good, turbulent mixing of the flue gases and consequently a better combustion process and burnout as well as proper filling of the first pass with flue gas. This results in better heat absorption in the boiler. Furthermore, VoluMix may also prevent recycling zones.
The whole plant was designed based on detailed computational fluid dynamic (CFD) calculations and analyses, which have also been applied in the development of the VoluMix system.
The impact of the VoluMix is shown in the extremely low content of CO and TOC in the flue gas, as these substances are indicators of the completeness of the combustion process.
The principle of the plant design is a midstream furnace followed by a boiler with 2 1/2 empty radiation passes and a horizontal convection part and economiser. The boiler radiation passes are protected against corrosion with refractory lining and Inconel®.