From The Leader in Clean Power Production Technologies
WtE Combustion Technology — Sundsvall Plant
Success Story
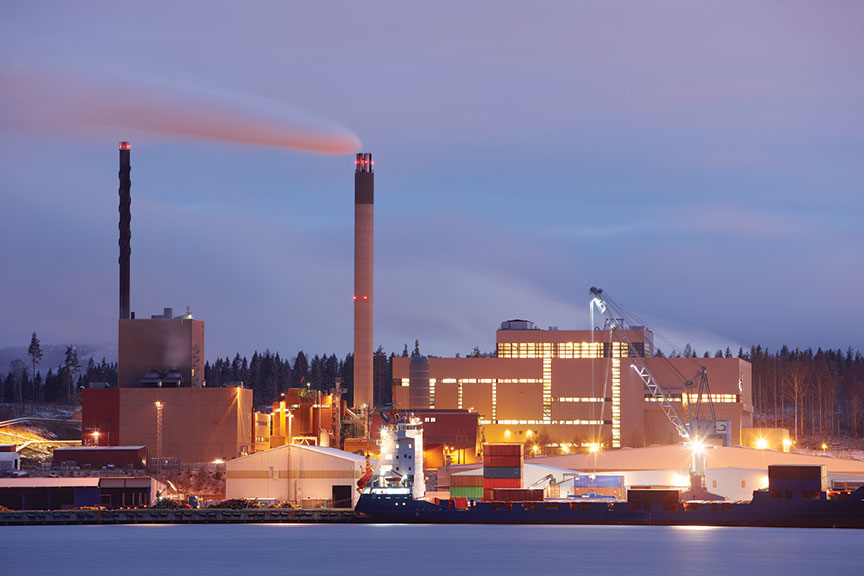
The contract for Sundsvall Energy’s new waste-fired power plant was signed in June 2004, and the plant was officially opened in March 2007. The new plant has a capacity of 25 tons of waste an hour corresponding to an annual operation of 200,000 tons.
The plant produces approximately 120,000 MW electricity and 300,000 MW district heating. The new plant was built next to the old plant.
Combustion technology
Babcock & Wilcox Renewable (B&W) supplied the Vølund® technology grate and boiler. The combustion grate is DynaGrate®, a two-lane air-cooled and water-cooled grate designed for fuels with high heating values.
The Sundsvall waste-fired power plant is the first plant with B&W’s new cast water-cooled grate bars. The boiler is designed with three-vertical passes and horizontal convection part. The maximum use of Inconel® for boiler protection limits the use of refractory.
Water-cooled wear zone
The Sundsvall plant is equipped with a water-cooled wear zone. The wear zone reduces uncooled refractory lining and thereby the built-up of slag. Advantages of the water-cooled wear zone:
- A water-cooled wear zone absorbs approximately 80-120 KW per m2. A typical system can receive 1.5-2.8 MW of extra energy - energy which is absorbed as radiant heat.
- There are no slag deposits as the wear zone is relatively cold, 120-250° C. The system therefore retains its active grate area throughout the operational period.
- Operational stoppages due to slag removal are not required. Heat absorption in the wear zone is 5-10 times higher than in the boiler’s two radiation passes.
- Heat absorption in the wear zone reduces the furnace temperature and therefore allows increased heating value and maintains waste capacity.
- The water-cooled wear zone replaces the refractory lining in the system’s most heavily used area and experience shows that a water-cooled wear zone has a longer life than refractory lining.
- It is possible to build in a water-cooled wear zone during a standard maintenance stoppage.
- The water-cooled wear zone works actively as an expansion segment between boiler and grate.
The heat absorption from the wear zone can be used in various ways:
- Directly connected to the boiler circuit: The wear zone is connected in natural circulation with the boiler drum and constitutes an integrated part of the boiler. This coupling increases the overall efficiency of the plant. Due to the high operational temperature, the wear zone must be covered with Inconel.
- Indirectly connected: The heat absorption is used for air or condensation preheater so that the plant’s efficiency is increased. The wear zone is executed in standard black boiler pipe.
- Externally connected: The heat absorption is used for district heating.