From The Leader in Clean Power Production Technologies
Waste-to-Energy Technology — Skærbækværket / Skaerbaek Plant
Success Story
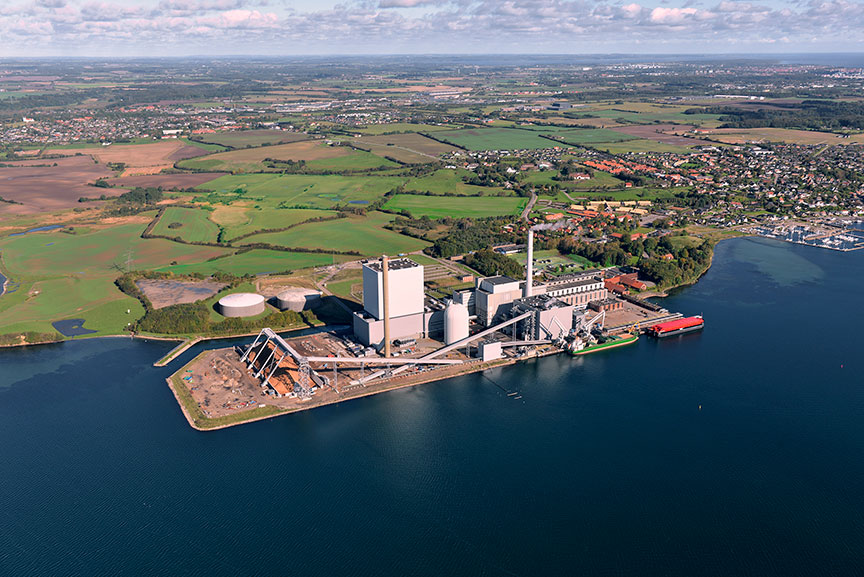
2 x 154 MW Biomass Boilers — Fredericia, Denmark
Babcock & Wilcox Renewable (B&W) designed, manufactured and commissioned two Vølund® technology biomass boilers for the Skærbækværket power plant in Denmark. The project allows the combined heating and power plant to supply approximately 60,000 households with clean and reliable district heating and electricity while reducing CO2 emissions.
Plant description
The Skaerbaek Power Plant (SKV40) is owned and operated by Ørsted A/S (formerly DONG Energy Thermal Power A/S). Built in 1951, the plant originally used coal as fuel. In 1997, it was converted to gas before the conversion to wood chips in 2014. The wood chips are sourced from sustainable forestry and help to reduce the plant’s carbon emissions.
Biomass as sustainable fuel for district heating
B&W supplied two identical 154 MW wood chip-fueled boilers, built on the harbor area in front of block 2 of the Skaerbaek plant. From the two boilers, a new steam pipe was established to the existing turbine of block 3 through which the boilers can supply steam for combined production of electricity and heat. The boilers are connected to a new heat exchanger for producing district heating independently of block 3’s operations.
Skærbækværket supplies about two-thirds of district heating to the municipalities in the triangle area that includes Fredericia, Kolding, Middelfart and Vejle.
TVIS, the district heating company in the triangle area, invested in the conversion of the Skaerbaek Power Plant to biomass with the goal of making district heating cheaper, greener and more sustainable, and 100% CO2 neutral and independent of fossil fuels by 2050.
The conversion to biomass is intended to reduce Skaerbaek’s CO2 emissions from district heating by approximately 83%. This is a reduction of 79,000 tonnes of CO2 each year.
Designed for flexibility and performance
The plant’s boilers were designed for maximum flexibility and performance. The boilers can utilize different fuels, and energy production can be controlled from a 25 to 100% load, depending on actual heat consumption or electricity prices. This allows the plant to maintain high availability when demand is high or adjusted in summer months when demand is lower.
To ensure the most efficient utilization of wet fuel, energy in the flue gas is captured in a condensing unit before the gas exits through the plant’s stack.
With this solution, the boilers are integrated into the existing plant and provide the highest degree of flexibility. Production output can be adapted to the district heating needs and market situation in the electricity market.
Scope of Supply
- Two 154 MW biomass-fired boilers
- Day silo for biomass material
- Firing equipment with airspout
- Vibration grate for each boiler
- Bottom and fly ash handling equipment
- Air preheating and distribution systems
- Galleries and stairs
- Building steel
- Instruments and cabling
- LV boards and PLCs
- Programming of the DCS
Grate design
B&W’s Vølund vibration grate has proven its performance on several recent biomass projects. Its high reliability and relatively low maintenance costs are attractive features for customers all over the world. The SKV40 grate is one of the largest ever built using this technology.
Boiler design
The boiler design is based on B&W’s experience in supplying solutions for specific high fuel flexibility. Fouling and high steam parameters were also considered. The 3-pass vertical boiler with slag tap superheater configuration has been proven at many installations.
Engineering the steam flow through the superheaters to minimize the steel temperature helps to minimize corrosion, wear and related outages and repair costs.