The B&W Learning Center
Leading the world in clean power production technology
Boiler Water and Steam Chemistry
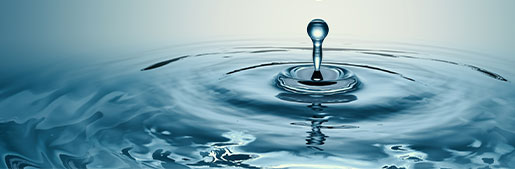
The Importance of Boiler Water and Steam Chemistry
Steam Purity
Purity or chemistry requirements for steam can be as simple as a specified maximum moisture content, or can include maximum concentrations for a variety of chemical species. Often, for low pressure building or process heater steam, only a maximum moisture content is specified. This may be as high as 0.5% or as low as 0.1%. Conversely, some turbine manufacturers specify steam condensate maximum cation conductivity, pH, and maximum concentrations for total dissolved solids, sodium and potassium, silica, iron and copper. Turbine steam must generally have total dissolved solids less than 0.050 ppm, and in some cases less than 0.030 ppm. Individual species limits may be even lower. If steam is to be superheated, a maximum steam dissolved solids limit must be imposed to avoid excessive deposition and corrosion of the superheater. This limit is generally 0.100 ppm or less. Even where steam purity requirements are not imposed by the application, dissolved solids concentrations less than 1.0 ppm are recommended at pressures up to 600 psig (4.1 MPa), less than 0.5 ppm at 600 to 1000 psig (4.1 to 6.9 MPa), and less than 0.1 ppm above 1000 psig (6.9 MPa).
For drum boilers operating up to 2000 psig (13.8 MPa), most nonvolatile chemicals and impurities in the steam are carried by small water droplets entrained in the separated steam. Because these droplets contain dissolved solids in the same concentration as the boiler water, the amount of impurities in steam contributed by this mechanical carryover is the sum of the boiler water impurities concentration multiplied by the steam moisture content. Mechanical carryover is limited by moisture separation devices placed in the steam path.
The formation of foam or excessive spray above the water line in the drum can cause excessive moisture carryover and therefore, excessive steam impurity concentrations. Common causes of foaming are excessive solids or alkalinity, and the presence of organic matter such as oil. Keeping dissolved solids below the concentration that causes foaming requires continuous or periodic blowdown of the boiler. High boiler water alkalinity increases the potential for foaming, particularly in the presence of suspended matter.
Where a chemical species is sufficiently volatile, it also carries over as a vapor in the steam. Total carryover is the sum of the mechanical and vaporous carryover. Vaporous carryover depends on solubility in steam and is different for each chemical species. For most dissolved solids found in boiler water, it is negligible by comparison to mechanical carryover at pressures less than 2000 psig (13.8 MPa). An exception is silica for which vaporous carryover can be substantial at lower pressures. Vaporous carryover depends on pressure and on boiler water chemistry. It is not affected by boiler design. Hence, if vaporous carryover for a species is excessive, the carryover can only be reduced by altering the boiler water chemistry. Only mechanical carryover is affected by boiler design. Noninteractive gases such as nitrogen, argon and oxygen carry over almost entirely with the steam, having no relationship to moisture carryover.
Excessive steam impurity concentrations can also be caused by feedwater and boiler water chemistries that favor volatile species formation. Carryover of volatile silica can be problematic at pressures above 1000 psig (6.9 MPa). Vaporous silica carryover at a pH of 10.0 is 88% of that at a pH of 8.8. The vaporous silica carryover at a pH of 11.0 is 74% of that at 8.8. The only effective method for preventing excessive silica or other vaporous carryover is reduction of the boiler water concentrations. Another common source of excessive impurities in steam is inadequate attemperation spray water purity. All impurities in the spray water enter directly into the steam.
Water Sampling and Analysis
Effective sampling is a key element in controlling water and steam chemistry. This includes obtaining representative samples, preventing contamination of the samples, and preventing loss of the species to be measured. In general, sample lines should be as short as possible and made of stainless steel, except where conditions dictate otherwise. Samples should be obtained from a continuously flowing sample stream. The time between sampling and analysis should be as short as possible. Samples should be cooled quickly to 100F (38C) to avoid loss of the species of interest. Sample nozzles and lines should provide for isokinetic sample velocity and maintain constant high water velocities (minimum of 6 ft/s [1.8 m/s]) to avoid loss of materials. Sample points should be at least 10 diameters downstream of the last bend or flow disturbance.
Detailed methods for chemical analysis of grab samples are readily available from the American Society for Testing and Materials (ASTM) and the American Society of Mechanical Engineers (ASME).
Wherever practical, online monitoring should be considered as an alternative to grab samples. This gives real-time data, enables trends to be followed, and provides historical data. However, online monitors require calibration, maintenance, and checks with grab samples or online synthesized standard samples to ensure reliability.
Adequate water chemistry control depends on the ability of boiler operators to consistently measure the specified parameters. Hence, formal quality assurance programs should be used to quantify and track the precision and bias of measurements. Detailed procedures should be in place to cover laboratory structure, training, standardization, calibration, sample collection/storage/analysis, reporting, maintenance records, and corrective action procedures.
Control of Water Purity to the Boiler
Because the local concentration of boiler water impurities and treatment chemicals is inherent to steam generation, water chemistries must be controlled so that the concentrates do not become corrosive. As an example, corrosion during operation of the boiler is often caused by concentration of sodium hydroxide, concentration of caustic-forming salts such as sodium carbonate, or concentration of acid-forming salts such as magnesium chloride or sulfate. Effective feedwater treatment, along with engineering controls, minimizes corrosion by minimizing ingress of these impurities to the boiler.
Carbon dioxide from air in-leakage and from decomposition of carbonates and organic compounds tends to acidify feedwater and steam condensate. Dissolved oxygen in the boiler system must also be controlled. Under most operating conditions, oxygen is especially corrosive because it facilitates oxidation of iron, copper and other metals to form soluble metal ions. At higher temperatures, oxygen is less soluble in water but the rate of chemical reaction is increased. The combination of oxygen and residual chloride is especially corrosive, as is the combination of oxygen and free chelant. However, in high-purity water systems, such as is used for supercritical boilers, the controlled addition of oxygen during operation is beneficial as it reduces corrosion product transport to the boiler and subsequently reduces the rate of deposition within the boiler.
Carryover of impurities from boiler water to steam is also inherent to boiler operation. Though separation devices in drum boilers remove most water droplets carried by steam, some residual droplets containing small amounts of dissolved solids always carry through with the steam. Also, at higher pressures, there is some vaporous carryover. Excessive impurities can damage superheaters, steam turbines, or downstream process equipment.
Boiler Feedwater
To maintain boiler integrity and performance and to provide steam of suitable turbine or process purity, boiler feedwater must be purified and chemically conditioned. The amount and nature of feedwater impurities that can be accommodated depend on boiler operating pressure, boiler design, steam purity requirements, type of boiler water internal treatment, blowdown rate, and whether the feedwater is used for steam attemperation. Feedwater chemistry parameters to be controlled include dissolved solids, pH, dissolved oxygen, hardness, suspended solids, total organic carbon (TOC), oil, chlorides, sulfides, alkalinity, and acid- or base-forming tendencies.
At a minimum, boiler feedwater must be softened water for low pressure boilers and demineralized water for high pressure boilers. It must be free of oxygen and essentially free of hardness constituents and suspended solids. Recommended feedwater limits are shown in Table 1. Use of high purity feedwater minimizes blowdown requirements in drum boilers and minimizes the potential for carryover, deposition and corrosion problems throughout the steam-water cycle.
Operation within these guidelines does not by itself ensure trouble-free operation. Some feedwater contaminants such as calcium, magnesium, organics and carbonates can be problematic at concentrations below the detection limits of analytical methods commonly used for industrial boilers. Also, operators must be sensitive to changes in feedwater chemistry and boiler operating conditions, and must adapt accordingly.
In Table 1 there is a distinction in pH control for plants that contain primarily ferrous materials and those plants that have feedwater heaters fabricated from copper-bearing materials. A mixed metallurgy system (ferrous and copper materials) complicates the specification of proper water treatment because the carbon steel requires a higher pH to minimize corrosion while the copper requires a lower pH to minimize corrosion. In a mixed metallurgy system, it is necessary to compromise pH levels to minimize the overall corrosion product transport rather than utilize elevated pH to control primarily iron corrosion product transport in the all-ferrous systems.