The B&W Learning Center
Leading the world in clean power production technology
Boiler Operations Part 1
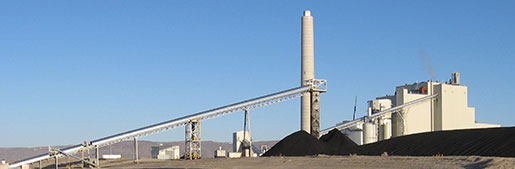
Boiler Operations That Affect Efficiency (Part 1)
In its simplest form, efficiency is the ratio of energy output to energy input, expressed as a percentage. To optimize efficiency, therefore, it is important to minimize input (fuel being a major source) and maximize output (steam production). However, these two goals often have opposing outcomes. This two-part article reviews the operator’s responsibility to effectively manage various techniques and key functions which will optimize efficiency, regardless of fuel or boiler type.
Part 1: Operating techniques for maximum efficiency
Fuel is a major cost in boiler operation. It is therefore important to minimize fuel consumption and maximize steam production. Although a boiler’s efficiency is primarily a result of its design, the operator can maintain or significantly improve efficiency by controlling losses to the stack and losses to the ash pit.
Stack losses
The total heat that exits the last heat trap is controlled by the quantity and the temperature of the flue gas. The quantity of gas is dependent on the fuel being burned, but is also influenced by the amount of excess air supplied to the burners. While sufficient air must be provided to complete the combustion process, excessive quantities of air simply carry extra heat out of the stack and result in a subsequent efficiency loss.
An operator can maintain or significantly improve efficiency by controlling losses to the stack and ash pit.
The temperature of the flue gas is affected by the cleanliness of the steam generator’s heat transfer surfaces. This in turn is dependent on sootblower performance and air heater operation. Optimal cleanliness of the heat transfer surfaces is achievable with advanced diagnostic and control systems that measure the heat transfer effectiveness of the furnace and superheater banks, evaluate against the design duty, and clean only on an as-needed basis.
While high gas temperatures exiting the last heat trap waste energy, excessively low temperatures may also be unacceptable. Corrosion can occur at the acid dew point of the gas where corrosive constituents in the flue gas condense on the cooler metal surfaces. Ash plugging of heat transfer surfaces in the air heater can be aggravated by the presence of condensate. Protection and performance of environmental components, such as an SCR, can also impose constraints on boiler exit gas temperature.
Pressures and temperatures
Most boilers supply steam to turbines or processes that require heat. These processes rely on specific pressures and temperatures. Deviations from the set points may result in lower overall efficiency of the power cycle, loss of production, or damage to the equipment or process.
In units that produce saturated steam, boiler temperature is directly related to the operating pressure. For many industrial applications, the process requirements dictate the steam temperature and consequently the operating pressure.
For electric power producing steam systems, steam temperature has a significant impact on turbine efficiency. Modern controls can typically maintain this temperature within 10F (6C) of the desired setting. For a supercritical pressure unit, each 50F (28C) reduction in steam temperature reduces cycle efficiency by approximately 1%.
Variable pressure operation
Historically, utility steam generators in the U.S. have been operated at a constant steam outlet pressure and the turbine load has been controlled by varying the throttle valves at the turbine inlet. This causes an efficiency loss at lower loads due to the temperature drop across the throttle valves.
In variable pressure operation, boiler pressure is varied to meet turbine requirements. This can significantly improve cycle efficiency when operating at low loads (15 to 40% of maximum continuous rating, or MCR). However, boiler response to turbine requirements is slower in this mode. When fast response is needed, pressure increments are used. At a given pressure, the throttle valves control the steam to the turbine and provide quick response. As turbine requirements increase and the valves approach full open position, the boiler pressure is increased to the next increment and the turbine valves are throttled back to provide some amount of pressure control. This arrangement provides high efficiency while retaining quick response.
In variable pressure operation, pressure increments are used to provide high efficiency while retaining quick response.
Emissions requirements
Component changes made to accomplish emissions reduction are typically accompanied by new operating philosophies and guidelines for efficiency and equipment protection. For example, to achieve the lowest possible NOx emission levels, the combustion system must be altered and flue gas temperature to the SCR regulated to a precise temperature window to maintain SCR efficiency and minimize ammonia usage and slip. To reduce the amount of NOx produced in the furnace by the fuel burning process, design changes to the combustion systems have progressed from circular high spin, high velocity burners, to low NOx burners with excess air, to substoichiometric burner air flow and staged combustion in the furnace.
Staging of combustion air is frequently used in firing system upgrades to reduce NOx emissions. Sufficient care must be taken to ensure that lower furnace corrosion associated with the reducing atmosphere is not excessive, especially with high sulfur fuels. Depending on system design, there may be tradeoffs between lower NOx generation and increases in the carbon content in the ash and CO in the flue gas. To maintain ash quality suitable for disposal or sale, operational balance must be achieved within the combustion process. Furnace combustion is also usually controlled to achieve a specific CO emissions rate.
Combustion optimization
A modern DCS offers a significant amount of information to assist operating personnel in optimizing steam generator performance. Closed-loop neural network systems and other advanced intelligent control systems have made strides in maintaining optimum combustion performance throughout the operating range. Variants of these systems use complex databases and algorithms to guide the controlling parameters during steady-state and transient operation. As long as no subsequent mechanical modifications are added and proper equipment maintenance is available, these advanced control systems are capable of consistently returning the steam generator to its optimum operating condition. A significant attribute of these systems is the ability to target specific results during optimization and change the targeted parameter as needed.