The B&W Learning Center
Leading the world in clean power production technology
Construction Project
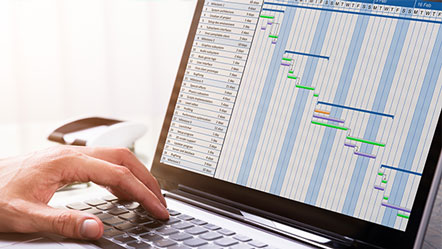
Construction Project Controls Primer
Project controls are used to deliver three primary goals:
- completion of the contracted work scope,
- performance to the contract schedule, and
- performance within budget.
The basic control process involves two steps:
- Step 1. A construction plan is created which details the work activities, manpower, time and equipment needed to complete the contract. The construction plan is tested to ensure that if the plan is followed, the three primary goals will be achieved.
- Step 2. As the work is performed, deviations between the construction plan and actual performance are noted. Deviations from the plan provide valuable information and a call for action to take advantage of favorable deviations or to correct unfavorable deviations.
Scheduling software is typically used to build and maintain the project schedules. All aspects of the project scope, material supply and erection, as well as balance of plant supply and erection, should exist within the scheduling software database.
Cost management software is used to integrate cost collection, time charging, expense reporting, work breakdown structure, procurement management, material receipt, accounts receivable, accounts payable, revenue recognition, and standard and custom report generation.
The master project schedule and all management and client reports are maintained and issued by the lead project scheduler. Regularly scheduled meetings with the project team can help identify any potential problems.
Project schedules emphasize the timely completion of required activities. The project plan should include a sufficient number of activities to monitor and control schedule performance. The activities should generally be of short (less than one reporting period) duration although there are some instances where this is not practical. Activities should be logically tied to predecessors and successors in a manner that accurately models the expected flow of work.
Measurement of construction progress can be achieved through an automated tracking system designed to provide an objective measure of physical percentage of completion for each activity of the project schedule. This is applied to the Earned Value Management Procedure (a project management technique for measuring performance and progress based on a standardized work breakdown structure [WBS] and a standardized set of rules of credit) and the actual results are then compared to the baseline to provide variance and performance reports for analysis.